Simulação de Processos
- António Sousa
- 2 de set. de 2022
- 6 min de leitura
Atualizado: 12 de jul. de 2024
INTRODUÇÃO
Ao longo do tempo, a abordagem ao desenvolvimento de processos, bem como as expectativas em relação aos resultados do mesmo, foram evoluindo. Naquela que pode ser identificada como uma primeira fase, o foco estava na capacidade de resolver problemas rapidamente, após a sua constatação, na prática. Para quem está familiarizado com a noção de desperdício, tal como é entendido no Lean Production System, estas ações de correção, num processo que acaba de arrancar, podem ser consideradas desperdício.
As organizações com maior experiência neste tipo de atuação rapidamente reconheceram a necessidade de evitar problemas de produção na fase de conceção do processo, tendo, por esta via, surgido várias abordagens como o Design for Manufacturing, Design for Six Sigma, 3P (Production Preparation Process), entre outros.
As abordagens referidas permitem identificar e evitar muitos problemas, resultando num processo completo e bem desenhado. Para a definição da solução são considerados vários aspetos, a saber: a voz do cliente (VOC), a voz do negócio (VOB), a priorização dos requisitos, a avaliação dos riscos e as possíveis estratégias de mitigação. O resultado é um ramp-up mais curto, um custo dos produtos mais baixo e a adequada capacidade do processo.
Apesar de todas as provas dadas por estas metodologias, não podemos deixar de nos interrogar sobre o potencial por explorar. Que aconteceria se pudéssemos experimentar mais, sem que isso representasse custos de materiais ou tempo de desenvolvimento? Como poderíamos preparar melhor o processo se o expuséssemos às variações observadas quotidianamente, na vida real?
SIMULAÇÃO DE PROCESSOS
O conceito da simulação de processo introduz uma componente de experimentação ainda na fase de desenho do mesmo, o que permite a sua otimização , sem que haja impactos indesejados em termos de perturbações das operações (execução de testes em processos existentes) e em termos de consumo de materiais/ocupação de equipamentos e colaboradores.

A experimentação pretende responder aos seguintes desafios e dúvidas, que podem surgir na fase de conceção de um processo:
É necessário investir numa nova máquina?
O processo atual pode corresponder às expectativas?
Como mudará o prazo de entrega em função de alterações nos turnos de trabalho?
Qual a melhor estratégia para a atribuição de recursos?
Qual o verdadeiro impacto da melhoria da qualidade no prazo de entrega?
Qual o impacto da variação nos resultados?
Como dar resposta aos desafios de um contexto operacional que cada vez mais muda com mais frequência?
Para levar a cabo simulações é necessário dispor de modelos, que são aproximações, com maior ou menor fidelidade, à realidade.
Podemos caracterizar os diferentes tipos de modelos através do gráfico seguinte, ao qual acrescentámos alguns exemplos a cada categoria:

Podemos descrever, ainda que de forma simplificada, os modelos estáticos como:
Modelos que não “executam” uma tarefa ou um algoritmo;
Modelos em que toda a experimentação e análise são executadas pelos utilizadores.
Em muitas atividades de melhoria contínua são utilizados, desde há muito tempo, modelos.
Os mapas resultantes de uma análise VSM (Value Stream Mapping) serão talvez, nos modelos estáticos, a aplicação mais conhecida.

Os modelos dinâmicos caracterizam-se pelos seguintes aspetos:
“Executam” uma tarefa ou um algoritmo;
Permitem muito mais experimentação em tempo útil e são mais adequados a problemas complexos;
Exigem, como se depreende, capacidade computacional.
Os modelos dinâmicos podem, por sua vez, dividir-se em 2 categorias:
Modelos dinâmicos determinísticos: determinam a resposta ótima dado um conjunto de restrições;
Modelos dinâmicos estocásticos: têm em conta a variação dos processos e das suas solicitações. Não são construídos para dar apenas uma resposta, ótima, ao problema.
Existem muitas soluções em termos de aplicações/software de simulação, como Flexsim, Anylogic, Extendsim, Arena, Process Playground entre muitos outros. No conjunto de soluções presentes no mercado identificam-se funcionalidades orientadas para a organização do processo (cenários, parâmetros, sequência de operações, distribuição de operadores), bem como outras direcionadas para a simulação física dos postos e estações de trabalho. Nem todas as soluções apresentam estas duas tipologias de função, enquanto outras cobrem todos estes aspetos e ainda lhe juntam o desenho e animação 3D do processo. Daqui se conclui que a seleção do software deve ser cuidadosa e ter em conta as necessidades de simulação, bem como a sua complexidade de utilização.
A simulação de processos, através de modelos dinâmicos estocásticos apresenta uma série de vantagens, de entre as quais podemos destacar as seguintes:
Permite explorar possibilidades – testar o impacto de variantes do processo, procedimentos ou afetação de recursos sem perturbar o normal funcionamento das operações;
Facilita a avaliação do impacto de mudanças nos parâmetros do processo;
Expõe o processo modelizado à variação da procura, à variação da eficiência dos equipamentos, à variação dos recursos;
Permite uma avaliação mais correta da robustez do processo, num cenário realista;
Ajuda a validar os resultados esperados e a antecipar riscos.
Podemos, ainda, identificar algumas dificuldades e obstáculos à implementação deste tipo de análise:
Complexidade: pode ser difícil modelizar todas as funcionalidades do sistema/pode ser necessário dividir o sistema em mais do que um modelo;
Requer tempo e meios – nem sempre o software é conhecido e utilizado com frequência, o que implica formar ou encontrar alguém formado. Também é fundamental o conhecimento da realidade, o que implica envolvimento no processo;
O problema pode ser mais fácil de analisar e solucionar com um método analítico;
A experimentação direta no sistema real pode ser mais rápida, económica e de baixo risco.
APLICAÇÕES PRÁTICAS DA SIMULAÇÃO DE PROCESSOS
A simulação de processos pode ser aplicada, com vantagens, em muitos cenários habituais na indústria, dos quais podemos destacar alguns:
Produção e Montagem
Determinar o número de colaboradores, máquinas e células necessárias;
Avaliar diferentes alternativas de planeamento da produção:
Determinar a capacidade de produção;
Determinar o número de contentores necessários;
Estudo de configurações de linha alternativas;
Definir a dimensão lote/fabrico;
Sequenciamento da produção;
Identificação da dimensão e localização dos espaços para “Em Curso”;
Balanceamento de linha;
Planeamento de intervalos e turnos.
Manuseamento de Materiais
Determinar a frequência de passagem do sistema de transporte assim como a sua capacidade;
Determinar a velocidade do tapete de transporte;
Determinar o número de colaboradores que recebem o material.
Logística e Transportes
Planeamento de rotas;
Dimensionamento do número de docas;
Avaliação de políticas alternativas de gestão de “stock”;
Estudo do impacto da alteração de um “hub” na rede;
Análise de diferentes políticas de gestão das filas de espera.
EXEMPLO DE APLICAÇÃO
Consideremos um processo industrial organizado em Pull, como o representado na imagem:
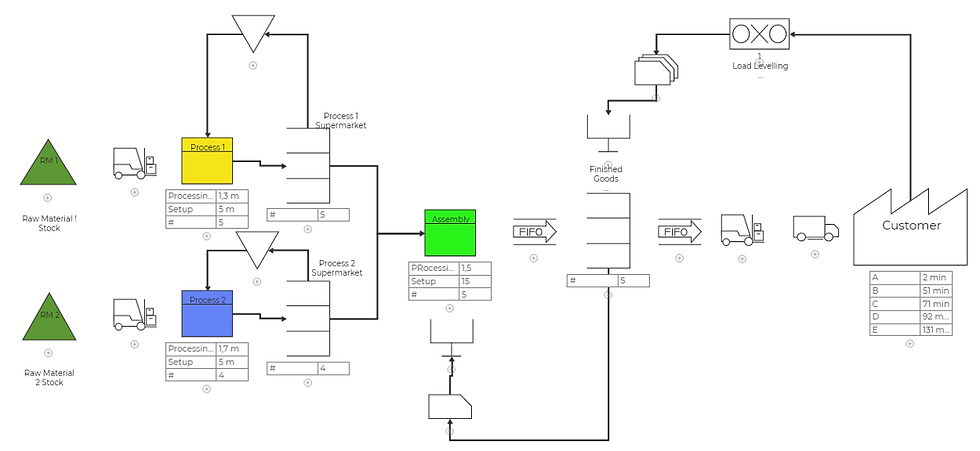
Ao “correr” a simulação e analisar os dados, constata-se o seguinte:
A procura foi totalmente satisfeita;
O supermercado (stock normalizado) de produto acabado cumpre a sua função.
Observando os níveis de stock, surge a questão: será que podemos ajustar os níveis de reaprovisionamento de forma a baixar o stock médio e manter o nível de serviço?

Alterados os parâmetros do processo e fazendo nova simulação verifica-se que sim:

E se quisermos saber como se comportará este mesmo processo quando exposto à variação da procura, à variação dos tempos de ciclo dos processos ou, ainda, à variação do tempo de setup dos processos?
Para construir este cenário é necessário alterar os parâmetros e, em lugar de valores fixos, considerar uma distribuição estatística para cada um deles. Assim, será necessário mudar o modelo passando do modo determinístico para o modo estocástico. Depois de correr a simulação, verifica-se que, quando sujeito a variação, o processo não tem um comportamento totalmente satisfatório, o que levará à necessidade de corrigir os parâmetros e fazer nova simulação:

Da mesma forma se poderia avaliar o impacto da redução do tempo de setup dos equipamentos nos stocks e no leadtime do processo.
Demos assim um exemplo, ainda que descrito de forma sucinta, do que pode ser a experimentação através de um modelo e das suas potencialidades.
EM SÍNTESE
A evolução das ferramentas digitais de simulação tem permitido uma maior difusão da sua aplicação. O aumento da potência computacional também permite a utilização de modelos mais complexos, bem como “correr” a simulação mais vezes e ter dados mais próximos da realidade. O próprio conceito de gémeo digital presente na abordagem 4.0 veio dar novo fôlego aos modelos de simulação. Ainda assim, o esforço pode ser considerável, tanto na preparação do modelo como na sua análise, pelo que a opção por estas ferramentas deve ser bem enquadrada com os objetivos e nível a atingir na conceção de novos processos ou na melhoria de processos existentes.
Comments